Overview
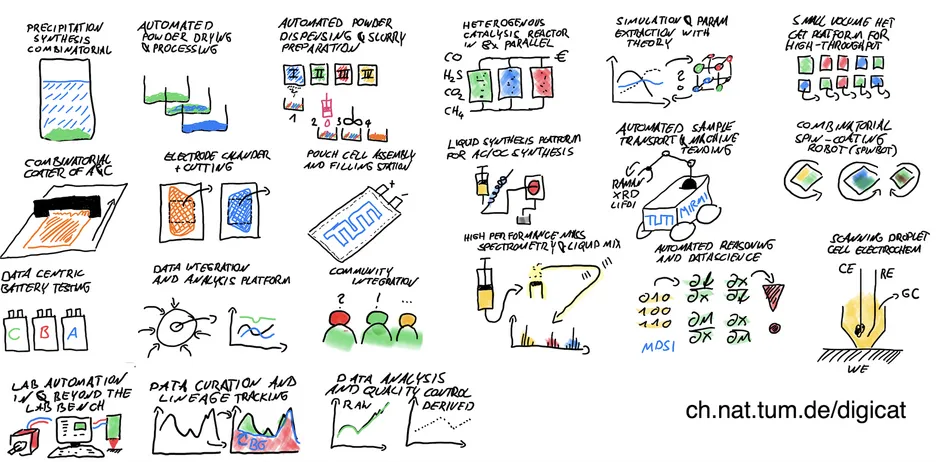
We are an experimental group specializing in high-throughput systems for synthesis, characterization, assembly, and recycling. By integrating automated experiments with theoretical frameworks, we address the entire research lifecycle—from materials synthesis to system integration. Our projects include the development of combinatorial synthesis machines, high-throughput characterization tools, agile manufacturing equipment, parallel chemical reactors, lab automation systems, Bayesian optimization methods, and explainable machine learning models.
Primarily based within the TUM School of Natural Sciences and aligned with the Technical Chemistry section, we also collaborate closely with the Munich Data Science Institute (MDSI) and the Munich Institute for Robotics and Machine Intelligence (MIRMI).
We research on the integration of bayesian optimization / uncertianty quantification with hardware and orchestration across labs to accelerate research for materials optimization but also to unravel new insights at a greater pace[1]. This entails of course benchmarking [1,2] of optimization alorithms and workflows and the development of domain specific optimization techniques[3]. We are specifically interested in the development of methods for uncertianty quantification that yields an estimate for aleatoric and episdemic uncertianty on both the predictions but also the inputs.
Contact persons: Aleksei Sanin
[1] Stein, Advancing Data-Driven Chemistry by Beating Benchmarks. Trends Chem. 2022.
[3] Rahmanian et al. One-Shot Active Learning for Globally Optimal Battery Electrolyte Conductivity. Batteries & Supercaps, 5, (10), e202200228
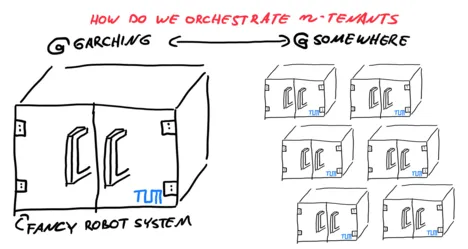
To develop a reliable materials acceleration platform for inter-lab [3,4] and intra-lab applications, it is necessary to focus on device-to-device communication, high-throughput data analysis and characterization, data management, and machine learning. For inter-lab communication, we have developed our asynchronous “HELAO” framework [1], which can execute experiments in sequential and parallel modes across one or multiple threads. This framework also includes an active learning server capable of selecting the subsequent experiment on the fly according to its acquisition function. For data analysis, the Python package "MADAP" [2] has been developed, which enables the examination and implementation of various electrochemical tests. These include electrochemical impedance spectroscopy, Arrhenius, and voltammetry analysis (CV, CP, CA). Additionally, in accordance with the FAIR principles, MADAP provides a comprehensive report, including all analysis steps from raw data that details all analysis steps, from raw data to their computed visualization. These two frameworks have been integrated into our most recent autonomous endeavor, Auto-MISCHBARES [3], which is additionally equipped with a PostgreSQL database, a quality control server for ensuring the reliability of the experimental steps at all times, a chatbot to inform the user about the experimental flow, a live visualizer, and a user-friendly user web interface. All three frameworks can be expanded according to the user's needs and are available in the GitHub repository [1,2,3].
Contact person: Fuzhan Rahmanian, Monika Vogler
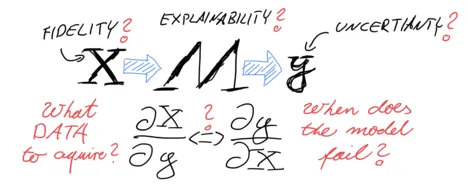
We love to do machine learning for chemistry beyond prediction of functional properties[1]. This includes accelerated data analysis[2], data curation[3] and, most importantly, visualisation[4]. We have been interested in human-in-the-loop machine learning for almost a decade[2]. The vision is to use some of these tools to develop a better -ML-enhanced - understanding of the underlying physicochemical processes[5]. We are active in both battery research and, more recently, catalysis. In battery research, we are mainly concerned with formation and non-linear charging schedules[6], and in catalysis we are investigating novel ways to catalyse and understand the production of high-value chemicals. We are also interested in using ML tools to explore the chemical space of stable and metastable compounds more efficiently [7].
Contact person: Helge Stein
We understand that a well-designed data management infrastructure is a key prerequisite for the efficient utilization of high throughput methods to enable machine learning approaches and data driven discovery of new materials and technologies [1]. Being at the forefront of research acceleration, the members of our team have embraced advanced data management practices [2,3] long before they became standard. Our approach emphasizes materials lineage tracking, ensuring that every step in the research process (including the data analysis! [4]) is accurately documented. By doing so, every processed result can be traced back to its corresponding raw data set in a transparent way. To achieve this, we actively contribute in the development of novel software tools and solutions. Our commitment to FAIR (Findable, Accessible, Interoperable, and Reusable) data practices fosters increased automation and autonomous discovery in materials and chemistry research. Further, implementing a lightweight data management framework, we have participated in building extensive databases containing raw data and metadata from millions of material synthesis and characterization experiments. Making such data sets available to a broad public we strive towards repurposing the results of our research to generate new insights by engaging the whole material science community. To push a cultural change at an early stage of education, we incorporate topics of research data management in our teaching. Here we explore various data management solutions (like NOMAD-Oasis, ckan and others) while also discussing fundamentals of data management plans, how to ensure interoparability by means of onthologies or even legal aspects and licensing (LV Nr. 0000004231).
Contact persons: Fuzhan Rahmanian, Frederic Felsen
[1] Vogler et al. Brokering between tenants for an international materials acceleration platform Matter 6, 2647–2665, 2023 doi.org/10.1016/j.matt.2023.07.016
[2] Soedarmadji et al Tracking materials science data lineage to manage millions of materials experiments and analyses npj Comp Mat 5, 79 (2019) www.nature.com/articles/s41524-019-0216-x
[3] Castelli et al. Data Management Plans: the Importance of Data Management in the BIG-MAP Project Batteries & Supercaps,4, 12, 2021 doi.org/10.1002/batt.202100117
[4] Rahmanian et al. Conductivity experiments for electrolyte formulations and their automated analysis www.nature.com/articles/s41597-023-01936-3
Combinatorial synthesis is an advanced materials research technique that involves the automated mixing of liquids and powders to synthesize large and diverse libraries of potential materials quickly. In high-throughput battery and heterogeneous catalysis research, robotic systems are used to accelerate the discovery and optimization of promising electrodes, electrolytes and catalysts materials.
We use the autonomous scanning droplet cell (SDC) setup in our group for the sequential deposition and precise electrochemical characterization of a large variety of thin film materials on a small scale using a single instrument. Robotic spin-coating (SpinBot) is another method we use to produce thin films with uniform thickness and composition. These techniques accelerate the process of material prototyping and analysis, enhance our understanding of material properties and behavior in various applications and significantly reduce time-to-market for new materials.
Contact persons: Aleksei Sanin
[1] https://doi.org/10.1039/D3DD00257H
[2] https://doi.org/10.1021/acs.chemmater.3c01768
[3] https://doi.org/10.1002/elsa.202100122
[4] https://doi.org/10.1016/j.coelec.2022.101053
[5] https://doi.org/10.1039/D3TA01217D
A cutting-edge robotic system has been developed to produce slurries from powders and liquids through gravimetric dispensing with a 6DOF (six degrees of freedom) robotic arm. This advanced automation platform provides precise control over the mixing process, ensuring consistent slurry composition and quality. After the slurry is formulated, it can be coated onto electrodes or other substrates using the same robotic system. The drying process is also automated, enabling high-throughput production of coated electrodes. Filming of this process is integrated to study the temporal evolution during the drying stage. The automation of these steps of electrode manufacturing allows for greater consistency and reproducibility than can be achieved with hand made electrodes in a small laboratory setting, and greater flexibility and agility than a large scale manufacturing plant.
Finally, the system is capable of cutting electrodes or coated sheets into specific sizes and shapes to meet various application requirements. This highly versatile robotic system can be used in a wide range of applications, including battery manufacturing and catalytic processes. The ability to produce uniform slurries with precise composition, combined with efficient coating and drying processes, makes this setup an essential tool for modern materials research and production in our lab.
Contact persons: Leah Nuss
Manual assembly of full cells is still the dominant manufacturing method in battery research, however, this conventional way confounds with digitalization and reproducibility in data-driven research for optimization of battery chemistry and cycling protocols. However, implementing an industry-scale pilot line battery production is resource consuming and lacking in agile. The intention is to build a bridge between singular man-made cells to the pilot line production of cells (system) and mitigate the obstacles in verification and translation in an academic research context to large scale deployments. We have pioneered lab scale battery manufacturing of coin cells1 and currently work on building a larger manufacturing system. The initial automatic battery assembly system (AUTOBASS) was able to build coin cells at 64 cells per batch using the same electrolyte. The second iteration2 uses active electrode placement and combinatorial electrolyte formulation thus further boosting the productivity and reproducibility. By utilizing that system, we demonstrated a non-conventional descriptor, which instead of focusing on either volumetric or gravimetric amount but the molecules amount per electrode surface area to study the impact of electrolyte additives on Li-ion batteries and fast formation techniques2,3. At TUM by integrating the High-throughput Combinatorial Synthesis as well as the High-throughput Electrode Manufacturing we are building up a "mini factory" as AB3 that is able to produce batteries from active material precursors and foils for multilayer pouch cells.
Contact person: Bojing Zhang
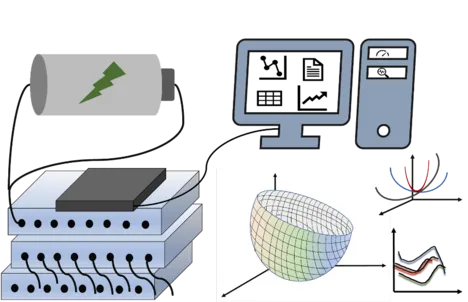
Battery test
We incorporate the battery test as the final step in our comprehensive automated battery production and assembly platform; through charging/discharging cycles and collaboration with conventional electrochemical measurement equipment platforms, full cell principles and performance can be thoroughly explored. Furthermore, derived from different battery test outcomes of various protocols in pure experiments, more extensive databases will be generated through data-driving simulation to solve time-consuming issues of battery tests.
Recently, we have been investigating the diffusion coefficient of batteries by utilizing the Galvanostatic Intermittent Titration Technique (GITT). Understanding and calculating the battery diffusion coefficient in electrode material is critical for optimizing cell design; in this part, all intricate data processes and related workflows rely on data-driving approaches to expedite battery analysis and cooperate with the automatic high-throughput battery system. Finally, the diffusion coefficient will be comprehensively demonstrated in detail based on different cycle protocols and temperatures.
In the thermal safety field of the battery, we combine numerical modeling with the science of battery materials, enabling us to develop our battery from its mechanism instead of constantly experimenting. This way, we can significantly reduce the expense of experiment stuff and become more efficient and targeted. To better establish and develop our model, an innovative temperature test platform is built which can proficiently capture the temperature and critical parameters of our battery.
Contact person: Jun Yuan
Parameterization
Parameter identification is a key aspect of battery modeling and simulation, enabling automation and efficiency in battery production, testing, and application processes; meanwhile, monitoring changes in key parameters facilitates effective battery fault diagnosis and health management can be carried out.
In this context, machine learning will serve as the primary method for parameter identification and weight evaluation. This approach can accelerate battery design and optimization by automatically selecting the best combination of characterization and cycle protocols. Similarly, battery research based on physics models, such as the Doyle–Fuller–Newman (DFN) framework, can also be significantly simplified by integrating data-driven approaches. This integration provides a deeper insight into understanding battery principles.
Contact person: Qiaomin Ke